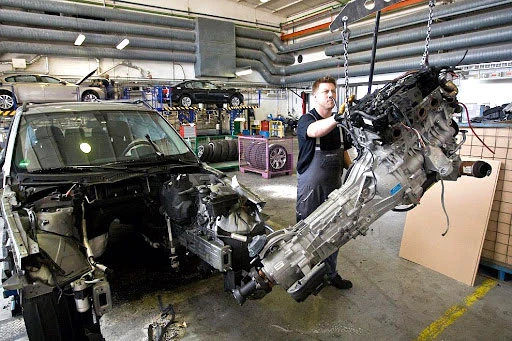
Hãng xe Volvo triển khai hoạt động tái sử dụng và tái sản xuất phụ tùng theo quy mô lớn. Quy trình của Volvo có tên Nguyên tắc kinh doanh tuần hoàn, bao gồm việc tái chế các vật liệu quan trọng như thép và nhôm, tái sản xuất các thành phần phức tạp như hộp số và cải tạo các bộ phận riêng lẻ. Trong năm ngoái, Volvo đã tái sản xuất khoảng 40.000 đơn vị phụ tùng, giảm phát thải 3.000 tấn CO2 và tái chế 95% chất thải sản xuất (bao gồm 176.000 tấn thép) để giảm 640.000 tấn CO2 ra môi trường. Tập đoàn ô tô đa quốc gia của Anh Jaguar Land Rover cũng có một dự án tái chế nhôm từ các xe phế liệu, qua đó có thể cắt giảm 26% lượng khí thải CO2 trong quá trình sản xuất.
Hãng BMW ở Lohhof, Đức tận dụng tối đa phụ tùng và vật liệu của xe cũ. Quá trình tái chế bắt đầu bằng việc đảm bảo an toàn cho xe trước khi bóc tách các bộ phận và linh kiện của chúng. BMW có cả quy trình hóa lỏng lốp thành cao su lỏng. Những linh kiện nào còn tốt sẽ được giữ lại, lưu kho và đánh dấu. Khung xe sau đó được đưa tới máy ép để ép thành một khối kim loại. Phần rác thải sẽ được thu gom và đưa tới khu vực tập kết riêng.
Công ty Indra, một liên doanh giữa nhà sản xuất ô tô Renault và Tập đoàn tiện ích Suez, tháo dỡ 5.000 ô tô mỗi năm để lấy phụ tùng. Công nhân xử lý bình nhiên liệu và tháo rời các bộ phận như động cơ, lốp xe, bảng điều khiển, gương chiếu hậu và các bộ phận khác của một chiếc xe trong vòng 2 giờ. Quy trình công nghiệp của Công ty Indra đã được đưa sang Bỉ, Bồ Đào Nha và Thụy Sĩ. Các bộ phận đã tháo dỡ của ô tô có thể được bán cho các cửa hàng sửa chữa hoặc người tiêu dùng. Phần còn lại được tiêu hủy hoặc tái chế để sử dụng trong các lĩnh vực khác.
Ngoài tái chế phụ tùng, các hãng sản xuất ô tô còn chú ý đến việc tái chế pin xe điện. Theo các đánh giá môi trường, việc tái chế pin có thể có tác động đáng kể đến nỗ lực bảo vệ môi trường, ví dụ như có thể giảm 25% nhu cầu đối với lithium, 35% đối với cobalt, 55% nikel và đồng vào năm 2040. Cha đẻ của pin lithium-ion Akira Yoshino, nhà khoa học được trao giải Nobel Hóa học năm 2019, khẳng định, tái chế pin là nhiệm vụ tiếp theo của ngành công nghiệp xe điện. Ở thời điểm hiện tại, các hãng xe đang hướng tới việc tái chế tới hơn 90% nguyên liệu cấu thành pin. Sau khi xả hết năng lượng, pin hỏng được nghiền nát và sử dụng những phương pháp đặc biệt để tách lithium, cobalt, mangan, nikel thành nguyên liệu thô.
Trung Quốc đang đi đầu nỗ lực tái chế pin, với việc nhà sản xuất pin CATL gần đây công bố xây dựng một nhà máy tái chế trị giá 32 tỷ NDT (5 tỷ USD) ở tỉnh Hồ Bắc. Công ty khởi nghiệp Thụy Điển Northvolt - đối tác của Volkswagen và BMW - có kế hoạch khai trương vào năm tới một nhà máy có khả năng tái chế 25.000 tấn pin/năm. Tập đoàn hạt nhân khổng lồ Orano của Pháp đang khởi động dự án áp dụng các kỹ thuật chiết xuất uranium để tái chế pin. Hãng xe Tesla của Mỹ tuyên bố 100% pin dùng trong xe điện của hãng là loại có thể tái chế và đang lên kế hoạch thiết lập cơ sở tái chế tại Thượng Hải, giúp giảm thiểu một lượng lớn chất gây ô nhiễm và thuế môi trường.