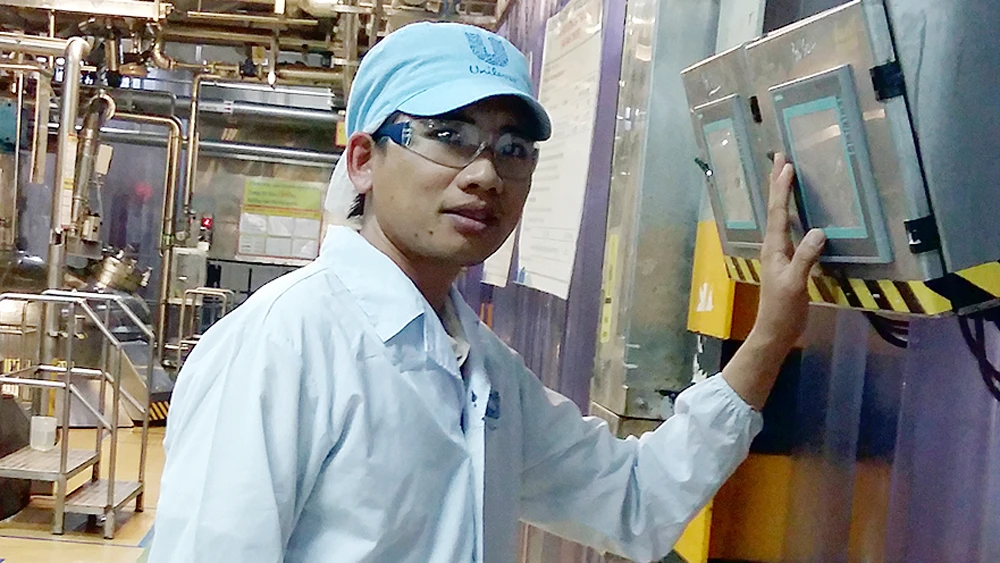
“Thời gian chuyển đổi mặt hàng sản xuất trên dây chuyền hiện nay vẫn còn 36 phút. Như vậy là quá cao, yêu cầu phải giảm xuống nữa, đề nghị anh em nghiên cứu, đề xuất”. Quản lý dây chuyền khuấy trộn Phan Văn Hây (Công ty TNHH quốc tế Unilever Việt Nam) đã đưa ra yêu cầu trên trong cuộc họp vào đầu tháng 3-2017.
Gần 1 tháng sau, anh em trong dây chuyền đưa ra 8 ý tưởng cải tiến quy trình này. Qua nghiên cứu, anh Hây thấy đề xuất dùng hóa chất thau rửa dây chuyền kéo giảm còn 20 phút (của anh Nguyễn Hoàng Phương và Nguyễn Minh Quyền) tuy đáp ứng được yêu cầu về rút ngắn thời gian nhưng việc sử dụng hóa chất sẽ gây độc hại cho công nhân thao tác. Do vậy, anh Hây tiếp tục nghiên cứu giải pháp khác. Sau 1 tháng mày mò, anh Hây đã thành công với công trình dùng hệ thống đưa nguồn nước đầu vào xả trực tiếp trên dây chuyền, thu gom được toàn bộ nguyên liệu bám dính trong thiết bị. Sau thời gian thử nghiệm, công trình đi vào vận hành. Kết quả thật bất ngờ, thời gian chuyển đổi sản xuất trên dây chuyền giữa hai mã hàng từ 36 phút xuống còn 7 phút, tiết kiệm cho công ty hơn 1 tỷ đồng/năm.
Không dừng ở đó, quản lý Phan Văn Hây còn đưa ra sáng kiến lắp đặt hệ thống thu gom nguyên liệu thừa sau khi chuyển đổi sản xuất mã hàng về bể xử lý riêng để đưa trở lại sản xuất, thay vì xả thẳng ra hệ thống thu gom, xử lý của nhà máy, vừa tốn kém chi phí xử lý, vừa gây tổn thất nguyên liệu. Với quy trình mới này, mỗi lần chuyển đổi mã hàng đã thu hồi được 130kg nguyên liệu, góp phần giảm 88% tổn thất nguyên liệu và làm lợi cho công ty hơn 1,7 tỷ đồng/năm.
Đó là 2 trong 8 sáng kiến của thợ giỏi Phan Văn Hây tham gia xét tuyển Giải thưởng Tôn Đức Thắng năm 2017. Điều đặc biệt là sáng kiến nào của anh cũng hướng đến mục tiêu cải thiện môi trường làm việc cho người thợ, nâng cao năng suất lao động, tạo ra giá trị mới từ những phế phẩm thải bỏ trong dây chuyền sản xuất, làm lợi cho công ty hàng tỷ đồng mỗi năm.
Trong đó, đáng chú ý là các sáng kiến: Giảm thời gian khuấy trộn sản phẩm Comfort Blue Conc từ 146 phút xuống còn 85 phút; tái chế sử dụng nước rửa sản phẩm Comfort; giảm 80% tổn thất nguyên liệu chất thơm trên dây chuyền 1001 khi chuyển đổi sản xuất…
Trong đó, chỉ riêng sáng kiến giảm 80% tổn thất nguyên liệu chất thơm trên dây chuyền 1001 khi chuyển đổi sản phẩm, mỗi năm tiết kiệm chi phí sản xuất cho công ty gần 3,3 tỷ đồng. Ở sáng kiến này, anh Hây đã dùng kỹ thuật và lắp đặt thêm thiết bị tách nguyên liệu chất thơm trong hỗn hợp nguyên liệu sản xuất Comfort của quy trình khuấy trộn. Mỗi ca sản xuất thu hồi được một lượng lớn chất thơm - loại nguyên liệu có giá thành cao nhất trong hỗn hợp nguyên liệu đưa vào sản xuất. Thành công của công trình này đã được công ty đầu tư lắp đặt trên toàn bộ dây chuyền sản xuất, đưa vào áp dụng chung cho quy trình tách nguyên liệu chất thơm và một số nguyên liệu giá trị khác, thay vì thu gom vào hệ thống xử lý chung như trước kia, vừa gây lãng phí và tốn chi phí xử lý môi trường…
Sau mỗi sáng kiến được ứng dụng vào sản xuất, Phan Văn Hây đều hướng dẫn anh em trong dây chuyền cách làm cải tiến, thực hành thao tác mẫu trên từng công đoạn để nâng cao trình độ chuyên môn, tham gia các đợt thi tay nghề trong công ty. Mỗi năm, anh còn kèm cặp, hướng dẫn tay nghề cho hơn 30 công nhân mới, giúp nhiều người trở thành lao động giỏi của đơn vị.
30 tuổi đời, 10 năm tuổi nghề, người thợ trẻ Phan Văn Hây đã có 3 bằng khen và 4 giải thưởng lớn do các tổ chức trong và ngoài nước trao tặng. Trong đó, chỉ riêng năm 2015, anh đoạt 2 giải nhất (1 giải quốc tế) về cải tiến kỹ thuật và kỹ năng tay nghề.